材木屋さんから購入する無垢材は、荒材なので平面を出さないと何もできません。
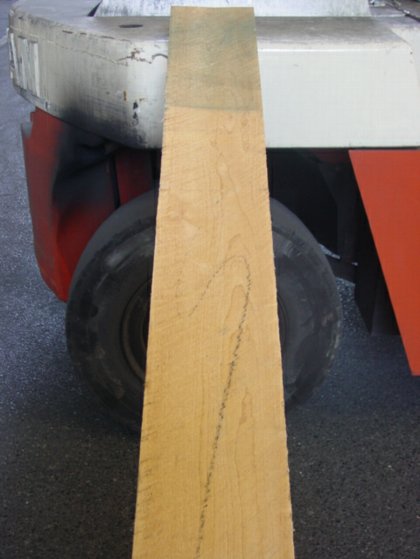
販売店によっては、プレーナー加工を有料で受けてくれるところもありますが、なかなか利用しづらい事もあります。
プレーナー加工を依頼するときの問題は、材の両端に段差(鼻落ち)が付いてしまう事と、研削によって想定した厚みが得られないことがある点です。段差はプレーナーの構造上仕方のないことなので、その分を見込んだ材料を用意して両端をカットするか、目立たないところに使用する必要があります。厚みの調整は、特にシナリのある素材を加工するときに顕著で、長い材料ほど、シナリの大きい材料ほど、切削量が増えてしまい、期待した厚みが得られない事があります。
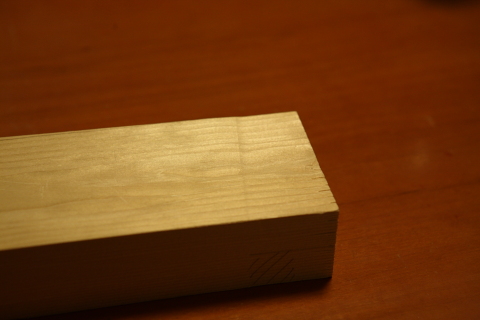
鼻落ちの例

この図は板材の断面です。黄色が荒材の断面で、茶色はプレーナー加工後に得られる板材です。上の板は、全体をプレーナー加工したときの図で、元の荒材に比べて得られる板材の厚さが、薄くなってしまっているのがわかると思います。そして、この両端5cmー10cmぐらいの位置には、プレーナー加工による段差(鼻落ち)が付きます。図の下側は、最初に長さ方向をカットしてプレーナー加工を行ったときの図です。同じようなシナリの荒材でも、もう少し厚みのある板を取ることができます。しかし、こちらも、それぞれの板の両端に鼻落ちが残りますので、長さ方向は使える部分が短くなります。
プレーナーによる段差(鼻落ち)ですが、性能が良く手入れの行き届いたプレーナーで丁重に加工すれば、ほとんど鼻落ちしないで加工することも可能らしいですが、材木屋さんにそこまで期待することはできないと思います。材木屋さんにプレーナー加工を依頼するときは、こういう点を踏まえて充分に余裕のある材料のときしか利用できません。
こんな具合ですし、材料には入り皮や節もあるので、実際に材料を見て板取りを決めないと無駄のない工作はできません。それに、無垢材は環境が変わると動くので、材木屋さんで正確に加工しても、自宅に移送すると、たいてい曲がって届きます。もっとも、自宅で加工しても、加工による水分量の変化や、内部に蓄積していた応力のバランスが変わることによっても変形するので、そもそもが一気に完成形の厚さまで切削する事は良いことではありません。私は、丁寧な加工する気分のときは、最終的な目的の厚さよりも、数mm厚く加工して数週間放置してから、もう一度切削して目的の厚さを作ります。The Musical Loudspeaker Project の時に使った側板は、仮切削後に、たしか冬の乾燥期に4ヶ月ぐらい放置しました。
そこで、自分で平面を出す必要性が出てくるのですが、私はいつもルーター加工で行っています。
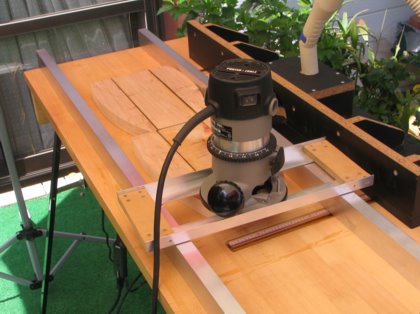
両側にアルミ製の角パイプを並べ、橋渡ししたジグの上でルータを左右に移動させて切削します。角パイプは3cm x 6cmの太さの物です。この写真では橋渡しに使っているジグもアルミ製ですが、今はMDF製のものに交換しています。アルミ材の上でルーターを滑らすと、ルーターのベースプレートが接触部だけが過剰に磨り減ってしまい都合が悪いです。
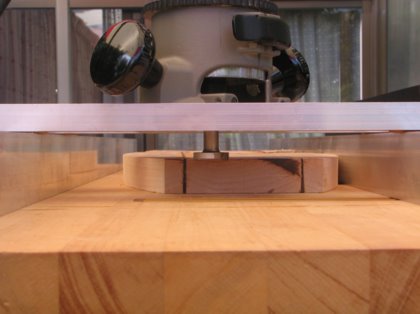
使用するビットは、Dado & Planer と呼ばれる物で3/4インチ径の物を良く使います。直径が大きいビットの方がきれいに早く加工できるように思いますが、実際にはそうではありません。こういう手作りのジグを、木製の作業台の上で使用すると、精度の問題からビットが正確に垂直に材料に接するわけではありません。極端に言えば、少し斜めになって接するので、切削跡はのこぎりの歯のようになります。
この、のこぎりの様になった表面は、サンダーで研磨すると消すことができます。しかし、ルーターのパワーによって木材の切削面が圧縮されている事があり、時間をかけてゆっくりと復元してきます。サンダーできれいに整えても、復元によって、後で再びルーターの切削痕が浮き出てくる事があります。これは、柔らかい素材の方が顕著で、針葉樹の加工の場合にはより一層の丁重さが必要となります。復元による切削痕の問題は、この作業だけではなく、木材にストレスをかける全ての作業に当てはまります。この問題は、サンダーを掛ける前に打ち水をして、強制的に復元させるとある程度軽減させることができますが、完全ではありません。できれば、加工後に1ヶ月ぐらい材料を寝かせて表面の様子を観察した方が良いです。
直径の大きなビット使うと、この段差が深くなるので返って表面の仕上げで時間がかかります。3/4または1/2インチぐらいのビットが作業時間と仕上がりのバランスが良いです。
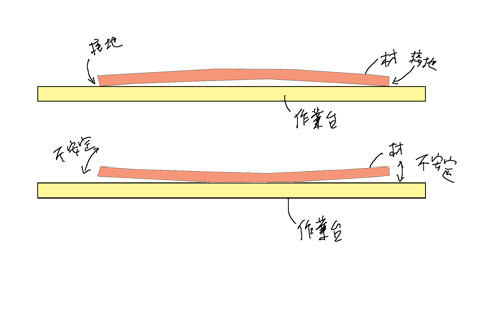
材料にシナリがある場合、上の図の上側のように、中央が膨らむように置くと安定しますので、先にその面を切削してから反対側を切削します。それでも安定が悪いときは、材料と作業台の隙間に、薄い板やスケールなどを挟んで安定させます。
材料の固定ですが、アルミのレールに楔で挟み込むと具合が良いです。適当な端材で、できるだけ材料がレールの中央に位置するようにして、両側から楔で固定します。このとき、レールを広げる方向に力がかかり、実際に少しレールが広がります。あまりレールが膨らむと具合が悪いですから、ほどほどの力で固定するようにします。切削は手前から奥に向けて行いますので、材料は奥に向かって逃げようとします。奥側だけしっかりと固定できれば、手前側はある程度ルーズでも問題ありません。
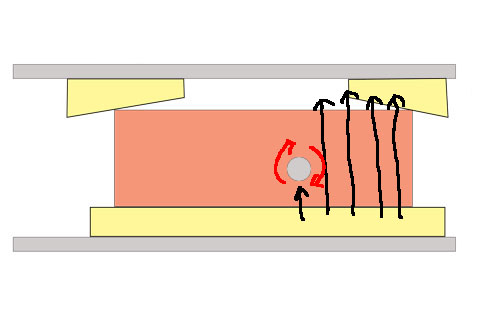
ルーターの移動は、このように右端から左端に向けて、手前から奥へ移動するときに切削するようにします。奥から手前に引くときに切削すると、ルータービットの回転方向と同じ向きに移動することになるので、キックバックのように思わぬ速さでルーターが走って危険です。左へ移動するときは、切削済みの部分とルータの刃の幅の半分以上重なるようにするときれいに仕上がります。つまり1往復で切削する幅は、3/4インチビットの場合で3/8インチ程度となります。
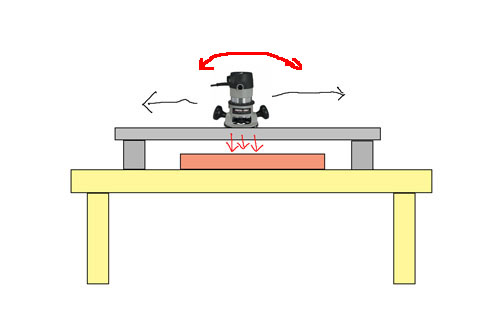
一度に切削する厚さは材料と期待する仕上がりにもよりますが、ハードメープルの場合で、だいたい1/16インチ(1mmから2mm)程度です。普通の荒材をきれいな板材に仕上げるには、3mm程度は切削する必要があるので、2回から3回の切削が必要です。
クセのある木材を切削すると、切削時に発生する熱によって切削面側に反ってくることがあります。また、逆に表面の乾燥した層が削り取られる事によって、テーブル側に反ってしまうこともあります。反った板を平面にするために行っている作業によって、反ってしまうのですから始末が悪いです。切削によって出た反りをそのまま無視して切削を進めると、想定以上に深く切削されてしまう事があるので、反りを確認したら即座に切削を中止して対策を行ってください。まずは、木材を休ませて見てください。少し放置しておくと元に戻る事があります。また、反ってしまった側を濡れ雑巾で拭いてやると戻る事もあります。いずれにしても、こうした木材の場合には、1回の切削量を減らして少しずつ切削するしかありません。
同じ厚さの板をたくさん作る場合には、両面を一度に切削せずに、全部の板の片面だけを最初に切削します。次に、全部の板の反対面を最後の1削りを残して切削します。そして最後に、全部の板の最後の一削りを行いますが、このときルータビットの突出量を絶対に変えてはいけません。こうすると、板材に隠れていたシミや入り皮も見えるようになりますし、どのぐらいの厚みが採れるか見当が付きます。また、最後の一削りをビット位置を変えずに行う事で、ジグの精度限界まで同じ厚みの板材が出来上がります。
切削時のルーターの移動ですが、できるだけ上から押さえないようにして、ルーターの自重だけが橋に掛かるようにします。どんな橋でも上から押さえつけると湾曲するので、材料の中央付近だけが深く切削されてしまいます。もっとも、湾曲する量は極僅かですので、見た目で窪んで見えるような事にはならないのですが、押さえる力が一定でないと、部分的に段差が生じて後の処理が大変になります。
しかし、あまり押さえつける力が少ないと、今度は切削時の反発で微妙にルーターがジャンプしてしまい、着地したときにルータービットの形に段差が生じてしまいます。ジャンプといってもこれも極僅かで、どちらかというと震動のようです。一度ジャンプすると、着地後の反発も強くなるので、ガッガッガッガッと連続した振動となります。
また、橋の上をルーターを滑らせるわけですが、このすべりがスムーズでないと、移動中に引っかかってルーターが振り子のようにゆれます。これが最悪で、傾いたビットによって深く材料が削られ、修復するためにはもう少し全体を切削することになります。この場合も、ガッガッガッガッと連続した振動となります。
面を切削するわけですから、大量のオガクズも発生しますので、オガクズにルーター移動の足元を邪魔されると、それも障害になります。
このように、ルーターでの平面加工は、切削量の多さもありますし、きれいに仕上げようとするといろいろと注意することが多いので、プレーナーに比べて非常に時間がかかり、神経も使います。その上、全面に切削痕が残るので、サンディングか手カンナで平滑に仕上げる作業も強いられます。
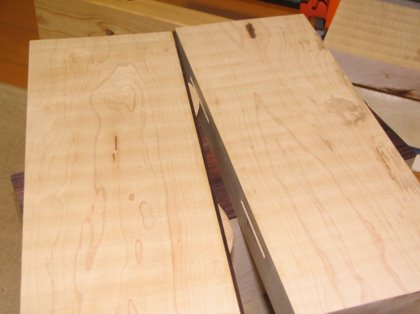
ルーターで加工した平面の例
プレーナーと比べてメリットなのは、当たり前ですがプレーナーがなくても加工できることです。プレーナーはそれほど高価な機械ではありませんが、重く大きいので私のような青空木工では使用できません。それと、プレーナーのように最大幅が決まっていないので、大きなテーブルなどの平面出しも可能です。それに、ちょっと違うかもしれませんが、橋やレールの形を工夫すればカマボコ型など、平面以外の形状も同じ手順で加工することができます。
結論としては、通常の平面出しではプレーナーの方が便利で早いので、可能であればプレーナーの導入をお勧めします。私も欲しいです。って、なんかTipsになってないな...